Glass, an Energy-Intensive Industry
The glass industry consumes a lot of energy. Whether it is flat glass or hollow glass, the first step is to melt the glass in an oven. Forming processes downstream of the furnace require temperature control at various points using burners and fans.
The result? High energy bills directly impacting your production cost (on average, 7 to 20%).
Are you looking to improve your energy performance? Solutions do exist!
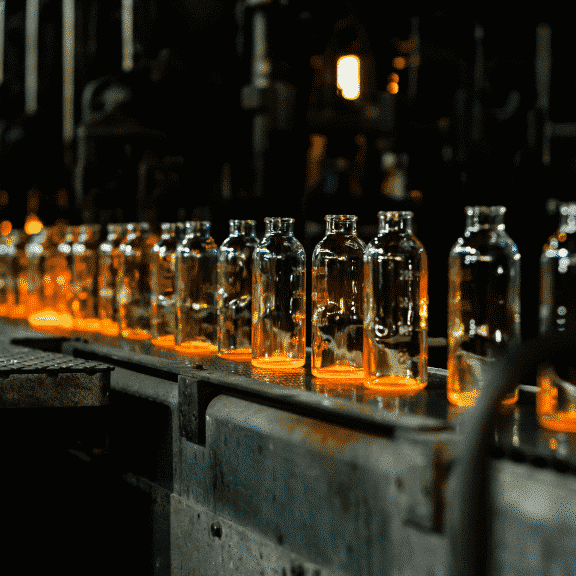
Digitalization to Reduce Energy Consumptions
METRON's energy intelligence platform digitializes and contextualizes all your influential data to make your plant more transparent.
The next step is to model your equipment (furnaces, etc.) according to their different conditions of use. The consumption model can also take into account the production context, energy prices or the impact of a refractory change on a day-to-day basis.
The platform provides informed suggestions on a daily basis to optimize your equipment settings according to your production objectives. You have a better control of your manufacturing process in order to continuously improve the homogeneity and quality of your products.
Examples of Data Collected in the Glass Industry
- Production (tonnage, glass type, etc).
- Power distribution on the different burners.
- Calcin.
- Temperatures on the different areas.
- Hygrometry.
- Operational parameters (production schedule, desired quality - prevention of bubbles in the glass, availability of raw materials).
Case Study in France: How to Save €250k in 1 Year on the Energy Budget from the Glass Furnace
One of the main French producers of hollow glass bottles wanted to optimize the energy performance of its industrial process without any investment.
METRON's solution enabled the company to digitalize and contextualize its data by taking into account all the influencing factors, and then to model the area to be optimized: the glass furnaces.
The manufacturer now benefits from real-time monitoring, enhanced control of its flexible parameters and alerts in case of deviations. It also receives suggestions for optimizing the setting of its furnaces according to production objectives.
The result? 10 GWh of electricity savings in 1 year, which is equivalent to a €250,000 saving on its energy bill, as well as a reduction in its carbon emissions of 1,900 tons per year.